Ever wondered what a semiconductor is and how they’re made? Or what KLA products are used for and why they’re so important to the industry?
Wonder no more because we’ve developed Chip Manufacturing 101, a beginner’s guide to explain how chips are manufactured and where KLA fits in the manufacturing process. Below, you can navigate through our interactive guide and learn about key steps in the chip manufacturing process.
The next time you wonder what semiconductor chip manufacturing consists of or want to share your knowledge, we hope you use this resource to understand KLA’s role in the chip manufacturing supply chain and how vital inspection and metrology systems are to chip production.
Chip Manufacturing
Microchip, chip, integrated circuit (IC), semiconductor chip, semiconductor device, microprocessor, silicon chip and computer chip are all interchangeable titles for the tiny objects that advance the world around us.
From cell phones, to cars, to artificial intelligence, chips are at the core of today’s technology. They enable the transfer of information and decision making for almost every technical function of our devices. The complex manufacturing processes these chips require are so precise that they must be checked for errors and defects from start to finish. This is where KLA’s systems become involved.
While chip manufacturing is an ever-growing craft in both importance and complexity, the natural beginnings remain the same.
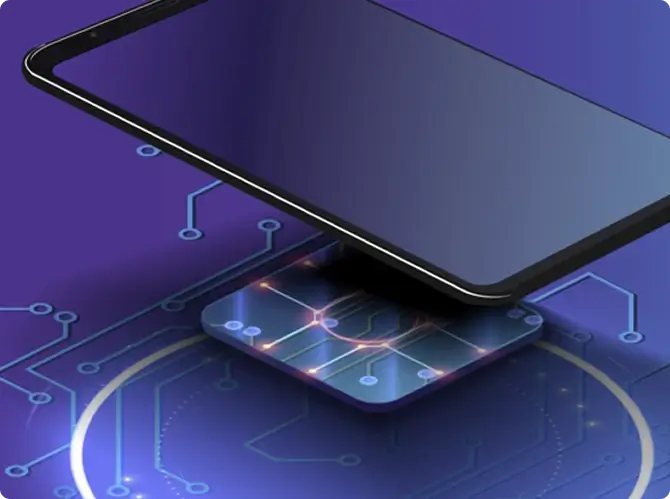
Sand: The Beginning
Building the chips that drive the world around us begins with the simple ingredient: sand.
What makes sand so valuable is its high concentration of the element silicon. Wafer manufacturing facilities house large furnaces that heat high purity silica sand to extract the silicon. Electronics require the silicon to be an even higher purity, so extra processing is necessary to ensure it is free from contamination.
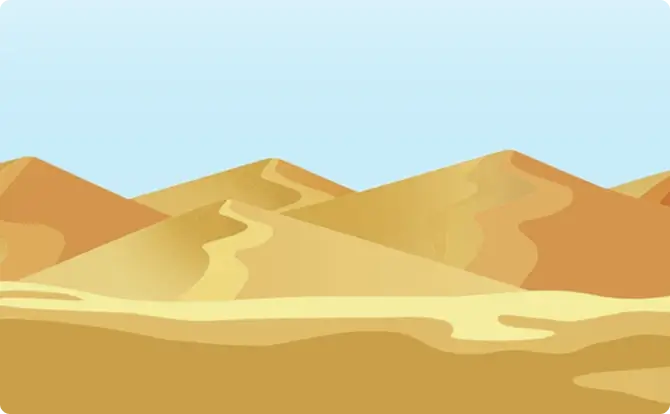
The Ingot and the Wafer
Wafers, the substrate used for the foundation of chip creation, materialize from a naturally cooled form of melted silicon called an ingot.
A seed crystal is placed on the surface of molten silicon to initialize ingot formation. As this seed crystal is pulled away from the silicon melt, it grows and bonds with the other silicon atoms in a lattice formation. This creates a single 1,000-pound crystal know as the ingot. Once perfected, this massive silver-colored cylinder is sliced into 1-millimeter thick disk-shaped wafers. These wafers are then polished to a mirror-like shine and inspected for defects and contaminants before they are sent off to a fab, where manufacturing of the chip continues.
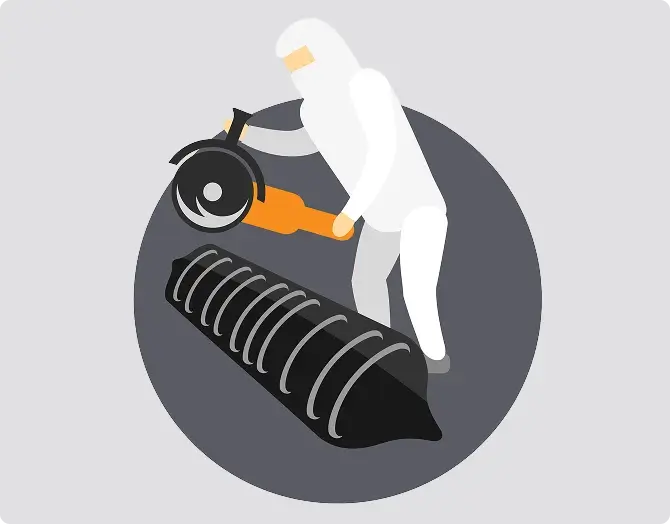
Fabrication Facilities and the Cleanroom Environment
A fabrication facility, or fab, houses the remainder of chip manufacturing and is where many of KLA’s products are utilized.
Because chips are fabricated on a microscopic scale with intricate 3D pattern designs, and consist of miles of tine electrical connections, the need to prevent contamination by dust and foreign substances is vital. Thus, inside the fab, considerable measures are taken to ensure sanitation, which is why many call it a cleanroom. Employees are required to wear full body “bunny suits” and hoods so that skin, hair, dust and clothing particles don’t contaminate chips or machinery inside the fab.
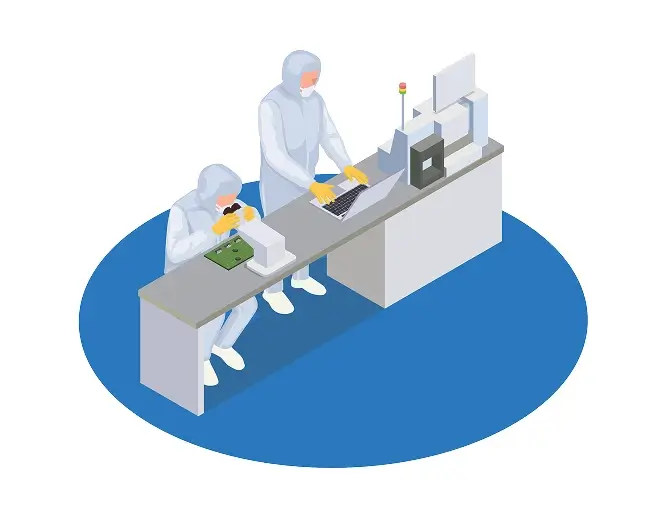
Silicon as a Semiconductor
Silicon is a key material within chips. It’s also how Northern California’s technology hub acquired the name Silicon Valley. But what makes it so special?
Silicon is a semiconductor. By bonding only with other atoms of silicon, a silicon wafer acts as an insulator. Yet, if small quantities of another element are added into the silicon structure as impurities, silicon can become an electrical conductor. The method by which this occurs is called doping. The type and concentration of the impurity determines the electrical properties of the silicon layer, as well as the functionality and proficiency of the final chip.
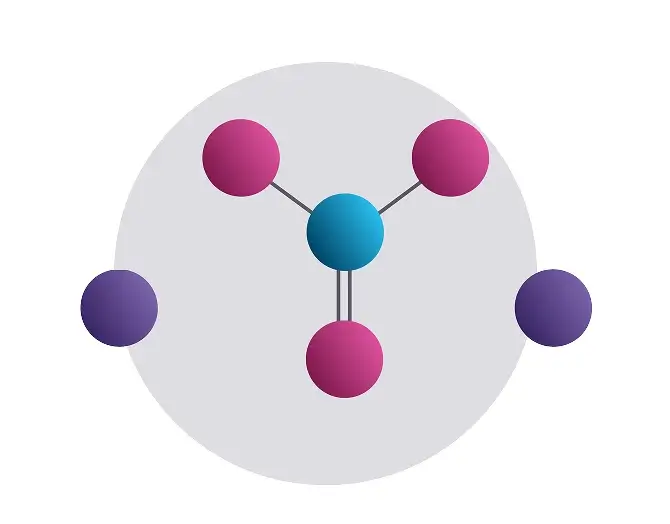
Transistors as a Power Switch
Three charged semiconductors, also referred to as doped silicon, are stacked together with varying charges between layers. This allows for a controlled flow of electrons, which makes up the next integral component of the chip: the transistor.
By applying current to the center of a charged transistor, the transistor acts as a switch, controlling the opening or closing of electric flow using binary code. One signifies on, while zero signifies off.
Today, despite silicon chips holding tens of thousands, sometimes billions, of transistors, they still fit into the palm of the hand. Chip sizes can range from a grain of rice to a credit card! Size, along with number of transistors and intricate design details, determine chip functionality.
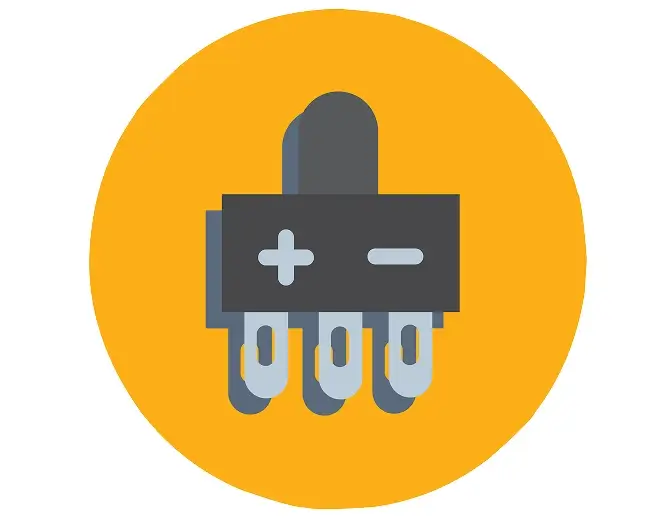
Assembling the Chip: Wafer Processing
Once fabs receive polished wafers from wafer manufacturers, each will undergo processing. This production cycle spans thousands of precise steps over potentially hundreds of machines to create the chips design.
Before processing begins, designers work behind the scenes crafting chip design patterns that will be printed onto reticles. Reticles, which are glass plates with etched-out circuit designs, are inspected, perfected and utilized in the first of several common processing procedures, which are often intertwined and repeated.
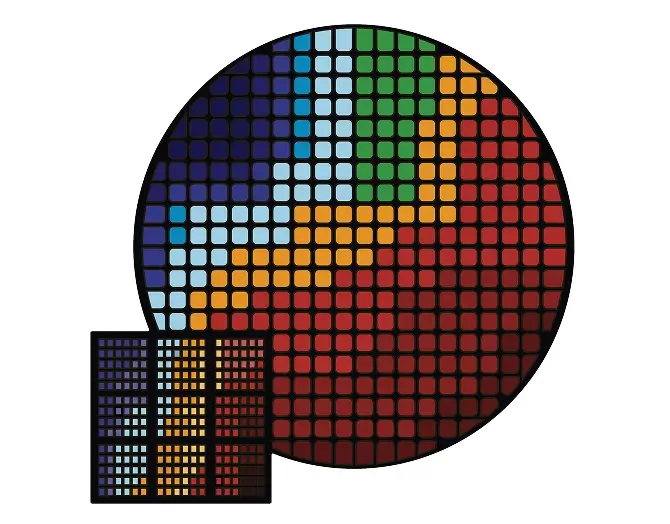
Photolithography: Transferring a circuit design from a reticle to a wafer.
- Light shines onto a reticle set directly above the wafer, which has been coated in a photosensitive material. The reticle’s etched-out pattern exposes specific areas on the wafer to the light, which reacts with the photoresist to create a pattern that will make up the circuits.
Deposition: Depositing a material using a variety of methods to creat a thin electrically insulating or electrically conductive surface on the wafer. The material type will determine the properties.
Plating: Coating the wafer to create a relatively thick metal layer.
- Plating fills holes and gaps between thin integrated circuits and helps establish connectivity across the entire wafer with a conductive metal material.
Etching: Removing unnecessary materials.
- The photoresist patterns established during photolithography form a protective layer, also called a mask, onto the wafer. During etching, a controlled chemical reaction occurs to etch away the unmasked wafer areas, transferring the required pattern into the silicon or the underlying material itself.
Doping: Altering electrical conductivity of certain areas on the wafer through the addition of impurities, usually in the form of gas.
Grinding/Chemical Mechanical Polishing/Planarization (CMP): Leveling the wafers surface.
- To make the surface flat and smooth, the wafer is mechanically ground then polished with CMP through the use of chemicals and mechanical processing.
The wafer processing procedures repeat numerous times, depending on each wafer’s design specifications. Process control operations are embedded in the cycles, checking for errors and contaminants to verify the success of each step and the ability to proceed to the next.
Process Control and the Value of KLA
As chip complexity increases and pattern feature size decreases, the chance of error, as well as the consequence of imperfection, become more substantial. This creates an escalating need for process control.
Throughout the entirety of wafer processing, KLA products are used to find and characterize errors which could weaken or wipe the functionality of chips. Defect sizes are often smaller than 10 nanometers. For reference, the width of a human hair is around 75,000 nanometers! With more than a thousand process steps required for every chip, and millions of chips being manufactured in fabs 24 hours a day, seven days a week, the need to automatically check and mitigate error is vital. Process control solutions, which detect defects and measure key features, make sure that the yields fabs produce are maximized.
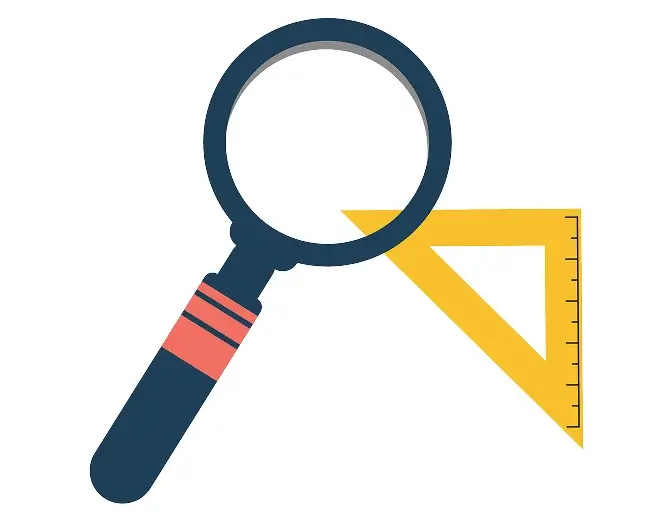
Process control can be split up into three main areas:
Inspection: Search for and detect defects or contaminants
Metrology: Measure to ensure the precision of the lines, etching, films and 3D features within critical chip layers.
Data Analysis: Characterize and analyze found errors so that a proper fix can be implemented. After solutions are applied to errors, these operations repeat until the wafer has a high yield of working die.
The Final Stage in Chip Manufacturing: Packaging
Packaging used to only be a means to protect and electrically connect chips, but has evolved into an intricate series of process steps that help increase the performance and capabilities of chips.
Advanced packaging schemes often require additional complex process steps on the wafer before it is diced. Once the processing is complete, wafers are tested to verify the electrical performance. Then the wafer is diced into thin rectangular pieces, known as chips. A single wafer holds anywhere between tens to hundreds of thousands of chips, with the number depending on specified wafer size and chip dimensions.
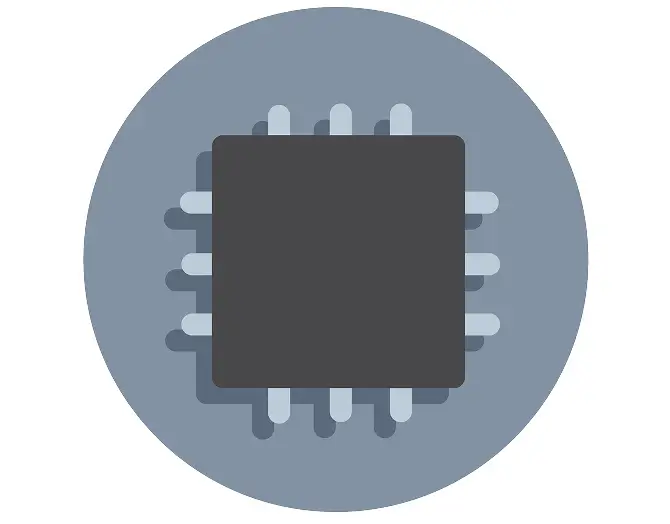
These individual chips are assembled into the final package where they receive a coating to protect their microscopic patterns and layers as well as wiring to enable their connectivity. Complex packages may include multiple chips combined! Process control steps play an important role throughout packaging to ensure the packages are high quality. A final electrical test to verify the functionality of the package completes the packaging manufacturing process.
Conclusion: Chips Enabling Technology
The chip manufacturing process is complete!
Now the fabricated chips are ready to be mounted onto a printed circuit board. From there, these chips will be assembled into almost every electronic device in the world. From the car you drive to the watch you wear, chips will enable the most innovative technologies, advancing humanity one device at a time. It is these precise steps, and the people who make it possible, that continue to drive and improve our world.
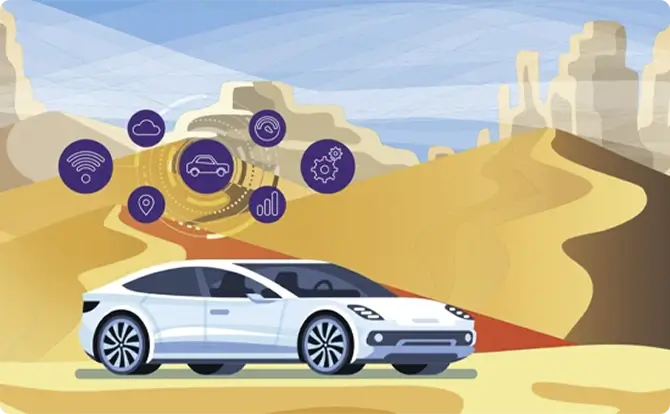
To download the Chip Manufacturing 101 guide, click here
Follow Us