Microelectromechanical systems (MEMS) are miniaturized systems that can be challenging to make and are relatively fragile. Often smaller than 1 millimeter, MEMS are built into components found in the electronics, automotive, medical and communications industries.
“As the name implies, MEMS involves the interaction of electrical and mechanical movement on a micro level. MEMS devices generally contain some freely moving mechanical part like a cantilever or membrane whose movement is induced by an electrical input or whose mechanical movement causes an electrical output.”
David Springer, research and development and product manager, KLA
As part of the MEMS manufacturing process, it’s critical to get those tiny parts moving. To do this, these microstructures must be supported temporarily by a “sacrificial” layer, usually made of silicon oxide or silicon. Once the device structure is complete, the sacrificial layer is removed to allow the MEMS microstructure to be “released” and move as required.

Silicon MEMS Release with HF Vapor
Sacrificial silicon oxide layers are typically removed by etching with hydrogen fluoride (HF) where Iiquid HF reacts with silicon oxide to form the gas silicon tetrafluoride (SiF4), plus water.
However, as this mixture or subsequent rinsing solutions dry, it can cause “stiction” by pulling the delicate, free-moving microstuctures together. These “stuck” structures remain permanently adhered to each other after release, reducing device yields. Another potential issue with wet HF etching is that the high concentration of water can corrode exposed metals, most notably aluminum, which is widely used on MEMS wafers.
To avoid these issues, dry HF vapor can be used. A gaseous etchant penetrates smaller features more easily than a wet etchant, allowing for smaller device designs with longer undercuts.
KLA’s Primaxx® VHF etch release process uses 100% anhydrous HF and ethanol for its dry HF vapor solution.
The ethanol ionizes the HF vapor and acts as a catalyst where everything stays in a gaseous state.
Water, a by-product of the reaction, also acts as a catalyst and is carefully controlled. With KLA’s Primaxx process that uses reduced pressure and elevated temperature, water is removed from the system. This process is available on multiple HF etch systems, ranging from the Primaxx uEtch for research and development to Primaxx Monarch series platforms for batch processing of 150mm to 300mm wafers in high-volume production. More than 200 Primaxx modules are being used by researchers and many high-volume MEMS device manufacturers.
Read more about KLA’s HF Vapor Etch solutions here.
Xenon Difluoride for Releasing non-Silicon MEMS
As MEMS get more complicated, they may contain components made from multiple or nonstandard materials. Devices can be made using any combination of silicon dioxide, silicon nitride, polymers, plus most metals and dielectrics. In these cases, the sacrificial layer may be silicon. Xenon difluoride (XeF2) can be used to isotopically etch silicon (Si), molybdenum (Mo) and germanium (Ge), and there is no other isotropic etch that is as selective to these three materials compared to most other materials.
Importantly, XeF2 does not attack most of the materials typically used in packaging or wafer dicing. As a result, XeF2 can increase yield by delaying the release of a MEMS device until dicing is complete or package insertion and wire bonding. XeF2 has been used successfully to release MEMS devices on diced wafers on the dicing frame and chips inside packages and offers very similar advantages as using HF vapor to etch silicon oxide. Click here to read more about KLA’s XeF2 solutions.
Advantages of Dry Release Etch Processes
Using the dry process eliminates stiction to optimize device yields without corrosion of aluminum bondpads. It also offers stable performance with a wide process window.
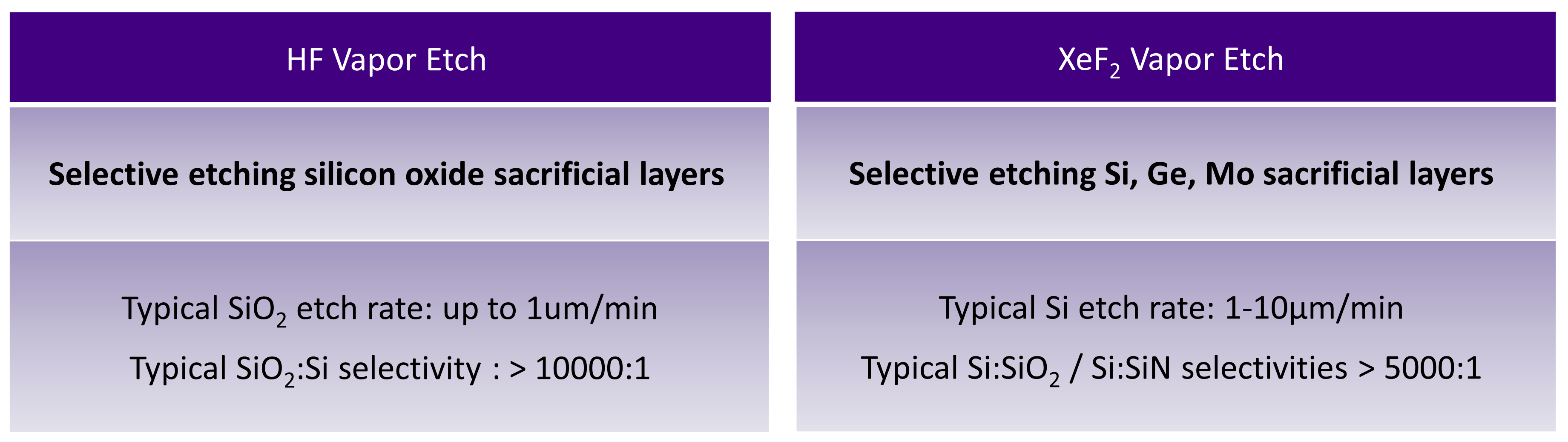
Application Examples
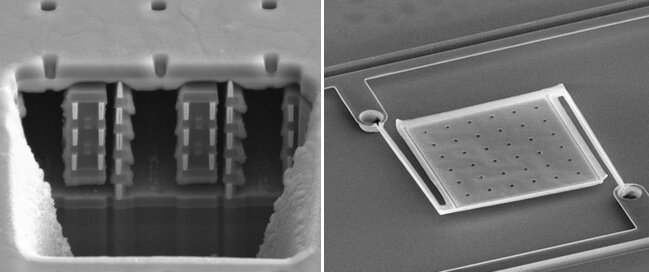
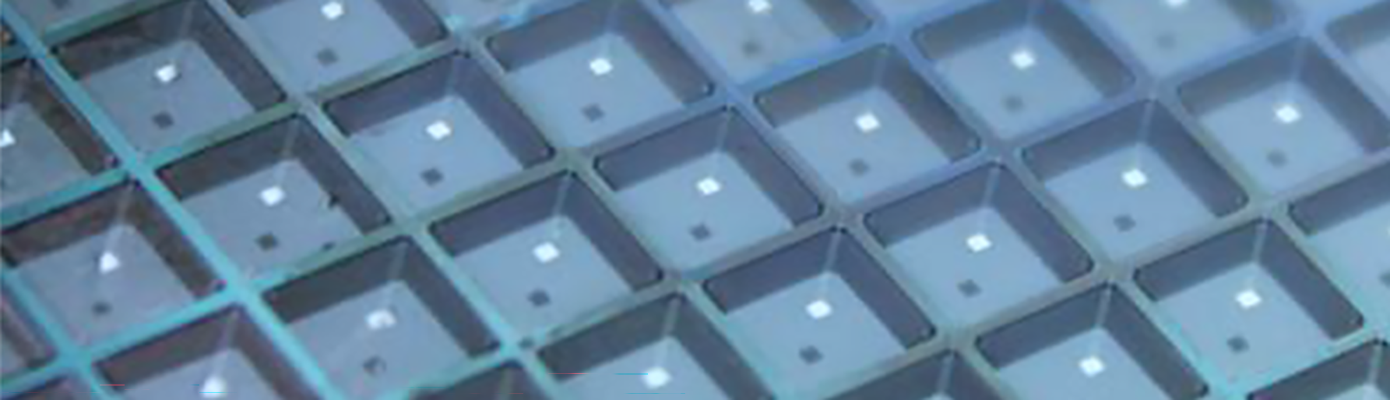
To learn more about the advantages vapor release etch can offer MEMS manufacturing processes, send us an email.
Follow Us