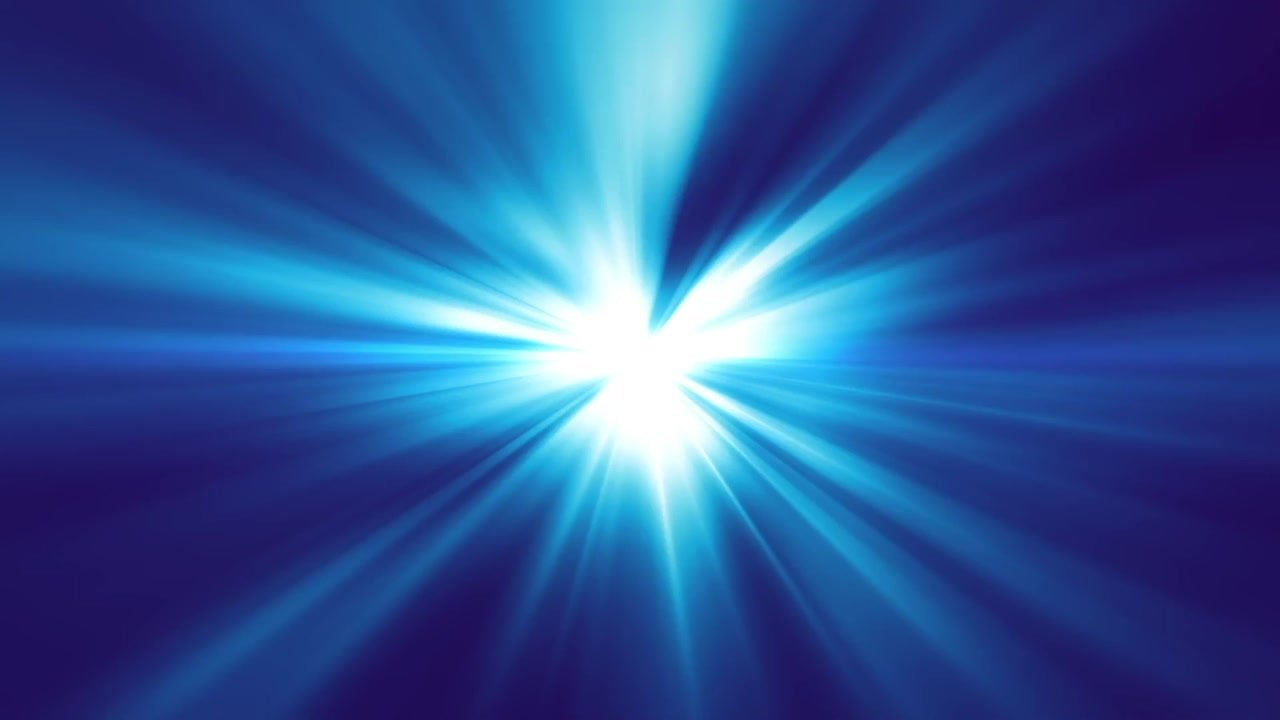
Video: MRAM
Dec 07, 2022Share This Page
MRAM combines the non-volatility of flash memory, the speed of SRAM, zero standby power, and has a density greater than SRAM. Learn more about MRAM as a promising universal memory and our metrology solutions to manufacture this exciting technology.